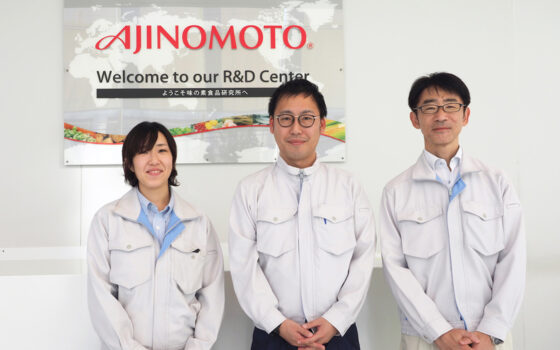
- Supporting Manufacturing
Above: Odawara Research Center
Below: Various products of Meiji
Meiji has two research locations, one here in Odawara and one in Tsurugashima in Saitama Prefecture. In Odawara we have three centers, the Food Development Research Institute, the Food Function Research Institute and Food Technology Research Laboratories.
The Food Development Research Institute mainly carries out product development, and the Food Function Research Institute conducts basic research leading to the development of new foods; for example, research on the functional properties of bacteria and their effects on the human body.
The Food Technology Research Laboratories, where we work, is engaged in comprehensive technology development research in a range of areas from basic ingredients to technologies for fermentation, production, and analysis and quality control, including not only the production and introduction of manufacturing facilities, but also quality control during production.
I'd never heard of particle method simulation software until I saw a demo applied to chips.
At the time, we had been producing a product that required putting lots of large pieces of fruit in yogurt, but there was variability in the amounts of fruit being filled and the challenge was how to transfer and insert the fruit in a uniform manner. We had studied the problem of mixing solids and liquids and had commissioned an analysis by another software company, but even after spending all that money we had no effective report to show for it, which was frustrating.
After going to an agency we'd worked with in the past for advice, we were introduced to SolidWorks Flow Simulation. Mr. Matsuki from Kozo Keikaku Engineering visited us and suggested that the particle method might be suitable for this problem. He showed us a demo using a two-dimensional particle method software system that was a sister product of Particleworks.
Simulation image of a U-shaped groove
The demo only lasted five minutes, but I was amazed by how well the software was able to manage coupled calculations of solids and liquids. Although I knew about calculations using particles, I hadn't known about analysis by the particle method, and I couldn't believe what I had just seen.
I had no idea even free surface flow could be simulated so easily.
We had made attempts to calculate free surface flow using complex methods, but seeing a demo of the flow being rendered like a cartoon and calculated in real time before my eyes, I was thinking "this is exciting, this is something we should make use of."
Seeing the image of churning chips, I was convinced that we could use this to analyze the mixing of yogurt and fruit, and I could imagine a wide range of other applications, so we immediately reviewed it inside the company and introduced the 2D version of the particle method software as well as SolidWorks Flow Simulation. That was in 2009. Six months later, we introduced the 3D version, Particleworks.
In 2D, we couldn't compute depth, and we couldn't handle numerical representations using actual physical property values.
We also couldn't make real-time calculations in 2D. On the other hand, being able to calculate the actual time, Particleworks allowed us to configure detailed settings and analyses based on real phenomena, such as specifying the mixing time in our manufacturing processes.
Representing splashing and spraying in free surface flow is a high hurdle for analysis, but the particle method makes even these phenomena easy to simulate.
Dr. Tetsu Kamiya
Manager, Ingredient Development Group,
Ingredient Development Department
Food Technology Research Laboratories
R&D Division
One scenario is the verification of new equipment to be installed.
With a new machine, you don't know what will happen. Particleworks lets us assess possible risks before installing equipment, bringing significant benefits in terms of cost reduction and efficiency improvement.
Another scenario is setting the optimal operating conditions of the equipment.
If there is too much mixing, it creates a vortex that can cause air bubbles, and the filling amount is reduced in proportion to the bubbles during product filling. By observing the free surface flow, you can set the optimal operating conditions of the tank to prevent bubbles.
Simulations using Particleworks have spread quickly through the company and are being used more and more for screening equipment. In addition, simulations are sometimes performed to develop solutions even after a machine has been introduced, for example when there is a malfunction.
We were not able to simulate it. We filled the cup at the factory, and then verified it by counting the actual number of fruit pieces. Because of variations in measurement, only qualitative trends could be observed.
Mixing conditions also vary depending on the viscosity of the yogurt. Even in cases where the physical properties change, Particleworks allows us to quantitatively evaluate the number of pieces per unit volume, which lets us simulate the degree of uniformity inside the tank.
SolidWorks Flow Simulation has its strengths and Particleworks has its strengths, so we apply them separately.
When we introduced a large tank in a production line for liquid food, Particleworks was good for the difficult calculations such as free surface flow, so we first created a 250-liter model to verify the risks of bottom mixing and eccentric mixing.
Next, we set the derived conditions in SolidWorks Flow Simulation and calculated the flow rate and time until completely blended. The reason we used them for different purposes is that although SolidWorks Flow Simulation can't handle the free surface calculation, it is easy to configure and the computations are fast.
In this case, we were facing two issues. The first issue was finding the conditions that prevented a vortex. And because it was a liquid food production line, the second issue was maintaining sterility from storage through filling.
"We make extensive use of Particleworks to improve problematic points
in newly installed equipment as well as in existing equipment."
Mr. Keigo Hanyu, System Engineering Group,
Production Technology & Engineering Dept.
On the first issue, generating a vortex, the eccentric mixer we were using just turned around and around in the same place, and took a long time to mix even while using a lot of power. To get a good mixture in a short period of time with the eccentric mixer, we had to use more than double the power we had been using and mix more vigorously, but that ended up creating a vortex.
We therefore introduced a new bottom mixer, but because this mixer was less powerful, we had to verify whether it could really mix properly. As a result of a simulation using Particleworks, we confirmed that because the bottom mixer was able to circulate a large flow up and down, it was able to mix effectively even at half the flow rate.
With respect to the second issue, because the bottom mixer turns the blades with a magnet, it has no parts in contact with the outside air, which makes it suitable for products that must be aseptically filled.
Analysis of free surface flow inside a tank by particle method
There's a team at Meiji studying quantitative evaluation of the throat, and we are working with them on a simulation of swallowing.
During the demo I mentioned earlier, when I saw the image of drainage in a clogged U-shaped groove, resembling objects dropped in a sink, I was struck with the idea of simulating the parts of the throat involved in swallowing food. Currently, we are using Particleworks to simulate ingredients to which thickening agents have been added (food products to aid swallowing). Since thickening agents are also used in hospitals and home care, these will be increasingly important ingredients in the future.
Swallowing simulator
Specifically, the analysis model is divided into four parts, the tongue, soft palate, pharynx and larynx. For each part, we configure the physical property values and other parameters at a fine-grained level to perform the simulation close to the actual movements.
We simulate how the tongue moves when food enters the mouth, and how the esophagus and respiratory tract work, and we run the simulation from the top, from the side and at various angles to see the conditions under which mis-swallowing occurs.
We are making a model of the human body from X-ray photographs from the hospital we are collaborating with, and measuring the physical properties of foods, such as viscosity and surface tension, and incorporating them into the analysis. When we present at academic conferences or give demos at a booth, academics often come up to us and say, "I've never seen that before! Stop it there and show me more!"
I'm also hoping to use the swallowing simulator in schools for food education. When they ask, "Why can't I swallow my food whole without chewing?", the answer is more compelling if you can see images of food that has gotten into the trachea.
In addition, with respect to families with seniors or disabled children, we have clinical knowledge of things like the appropriate viscosity for thickening agents, and how you can tilt the body in this way to prevent mis-swallowing and so on, but it's easier to communicate this information if you make a video using Particleworks, so we're looking at how to make effective use of this simulator.
Qualitative comparison of swallowing imaging vs. simulation
Quantitative comparison of swallowing imaging vs. simulation
Our company is making efforts to increase the opportunities for young people to experience analysis in order to broaden its appeal. Kozo Keikaku Engineering Inc. has helped us to take advantage of analysis tools, and in the future we would like to receive comments and advice from Kozo Keikaku, which has an engineering backbone. We appreciate your guidance.
In addition, in creating the swallowing simulation, we requested customization from Prometech Software, who makes Particleworks. We were able to customize it as desired and develop the swallowing simulation thanks to Kozo Keikaku Engineering Inc., who after understanding our needs based on their accumulated analytical experience and engineering expertise, got together to work with us on many occasions. With respect to our customization, which was unusual, Kozo Keikaku made clear what was possible and what was not, and then suggested a way to customize the software to enhance its maximum usefulness, and we were very grateful to receive such earnest support from them.
Interviewed in October 2012
SBD Products & Services Dept. SBD Engineering Dept.
TEL:+81-(0)3-5342-1051
E-mail:sbd@kke.co.jp
Web:https://www.sbd.jp/