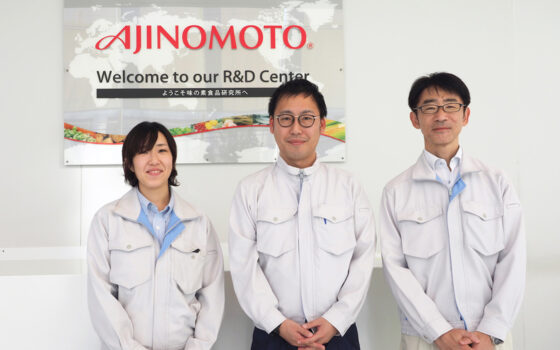
- Supporting Manufacturing
Most of our products consist of "powders", such as seasonings, soups etc. We are working on particles design to enhance the function of the powder and the technology to control the physical properties of the powder for a better product, but in fact the behavior of powder is quite tricky. For example, if liquids are mixed, basically they are maintained at a homogeneous mixture state. Whereas for powders, it is possible for segregation to occur. As a result, the powders may not be mixed evenly and the product might need to be discarded.
Experiments are carried out in a small scale to find the solution for this issue, but it may not work well when it is scaled up for an actual machine. As a result, the experiments have to be conducted all over again, resulting in a waste of time and raw materials for the trial and error process.
Kazuaki Shibuki
At the time when I was looking for a more effective way to solve this issue, I have learned about powder simulation technology at an academic conference. With the guidance of Dr. Mikio Sakai (Associate Professor at System Resilience Engineering Research Center, The University of Tokyo), we considered the applicability of the simulation software to our assignment for a year. As a result, the powder simulation software iGRAF was introduced. Simulation software from other companies were also considered but iGRAF impressed us with its simple and intuitive operational method.
Other companies provided trial version and also trainings but it seemed difficult to set the simulation parameters or run the software without relying on them. On the other hand, iGRAF can be easily used by learning the software tutorials. This is why iGRAF is chosen.
The common processes of various powders are mixing, discharging and filling. We have started with the analysis of storing and discharging process of a hopper.
The powders that we are using are smaller than 1mm. With the simulation, we do not expect that the phenomenon to be reproduced perfectly as extremely difficult calculations are needed in order to use the original particle size. For example, cases A, B and C with different conditions are simulated to find the worst condition. If the process can be practically reproduced to find the worst condition, two-thirds of the cost of stopping the production line for testing purpose can be reduced. This is the most significant benefit of this software.
Also, if devices with different shapes are to be tested, it takes several months to produce the devices. Even the test devices are ready, experiments and analysis require time, too. With iGRAF, however, the results can be obtained within a week. Time reduction is also one of the notable benefits of this software.
Sumi Yamazaki
Choosing a user-friendly software was important for us because it would be better if the software can be widely used within the company. We are at the first stage of using the software, and we aim to solve all the problems arise from the manufacturing site. Therefore, we have started to share the experience of using iGRAF with the colleagues in Institute of Food Sciences and Technologies.
After showing the simulation animation to my colleagues, we received many feedbacks saying, “The powder behavior is similar to the actual one”. Moreover, other researchers who have only experienced experiments were showing interest on the software and commented “Maybe this can be applied to that”, “Can you simulate something like this”, etc.
I agree. It is known to be difficult to calculate with the actual size of the particle, but we would like to accumulate the know-how of the simulation in order to overcome it.
One of the ways to utilize the software is to solve the problems arise from the manufacturing site. Besides, we can accumulate the basic knowledge of the optimal operation conditions of the equipment that we are using. Although repeating the tests by using equipment is common in the industry, wouldn’t it be better to do it at a lower cost? In other words, the decisions based on experiment experiences can be replaced by the physical theories.
Takeshi Nishinomiya
Eventually, we would like to take the result of the simulations as a reference to design the equipment. We are aiming for an environment where simulation is commonly used for engineering, such as having a discussion like “We should design a stirring device for the mixing of small and large particles” or similar topics. First, there will be an improvement on the existing equipment and we would like to put into action using the simulation result as soon as possible.
We really appreciate the support that you have given to us whenever we face troubles. As iGRAF is released for only a few years, we think that the functions will be upgraded steadily from now on and we are looking forward to it. We appreciate your continued support.
Interviewed in November 2018
SBD Products & Services Dept. SBD Engineering Dept.
TEL:+81-(0)3-5342-1051
E-mail:sbd@kke.co.jp
Web:https://www.sbd.jp/