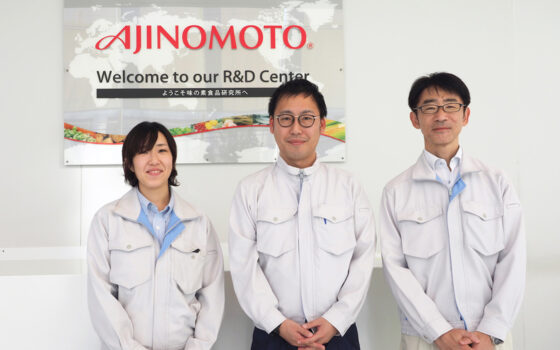
- Supporting Manufacturing
Ikuo Kawashima,
Project General Manager
of Production Engineering
Dept.
Takahama Plant, TOYOTA INDUSTRIES CORPORATION obtains a top-class market share around the world for products such as lift trucks and car air-conditioning compressors. There are 10 plants in Japan, including Takahama plant that specializes in productions of lift trucks.
There are many types of buildings in the plant premises. For our first reinforcement project, we chose a few of factories and laboratories that were built based on the old seismic code.
Regarding prevention measures against earthquakes, each plant and office decides which building should be a priority and takes actions. The discussion for conducting reinforcement for factory A came up in an early stage since it had the largest building area and a high density of workers.
As you may know, the Japanese seismic codes, the Act for Promotion of Renovation for Earthquake-Resistant Structures of Buildings, require a building to have a "Is (Seismic Index of Structure) more than 0.6*". For buildings that don't meet the index are considered as "necessary to increase seismic resilience". That is to say, the government is asking to conduct a seismic retrofit that meets the Is value of more than 0.6.
At first, we considered satisfying the value of Is. There were, however, detailed questions from the executive managers about the index such as "What are the difference between 0.55 and 0.6?" and nobody could give a precise explanation to it. We asked the general contractor "If we had a value of Is over 0.6, the building will survive a major earthquake, right?" but they never gave a 100% assurance.
Leaving the question up in the air, the seismic retrofit plan for the factories came out in the summer of 2014. The retrofit would take 15 years only for factory A, in total 18 years including other factories and labs. This construction period and the cost were not something that we have expected.
Takayuki Nishitani,
Manager of Production
Engineering Dept.
It was not a realistic prevention plan against a major earthquake, which might hit any day. The executive managers requested if we could have a different plan with less construction period and cost.
That was when we asked KKE for its support. We heard that KKE specializes in building structures and seismic solutions, and one of our plants have asked to run a simulation of seismic retrofit in the past. By using simulation once again, we hoped to receive clues that protect the buildings from seismic wave with a cost-effective manner.
Some executive managers asked us why it had to be KKE and that they needed more objective information about KKE. We understood these requests since running a simulation was not extremely expensive but was still costly. We thought that words would not be enough, thus presented the managers with the fact that KKE has achieved an excellent performance in a competition that used an actual building**. Participants competed over analyzing the seismic responses of a building by running a simulation and compared the result with the actual responses of the building. This fact served as a persuasive argument.
*1 Is (Seismic Index of Structure)
Is is a standard value of seismic performance which is calculated based on seismic strength, seismic ductility and aged degradation of structures.
It is described that against an earthquake of intensity 6-7, a building with the value of Is more than 0.6 has a lower risk of collapsing or being destroyed in the Act for Promotion of Renovation for Earthquake-Resistant Structures of Buildings, No.184-185. (established by Ministry of Land, Infrastructure, Transport and Tourism, 2005)
(Citation for Japanese Seismic Diagnosis Association -Japanese only http://www.taishin-jsda.jp/is.html)
**2 Blind Analysis Contest on E-Defense, 2009
KKE participated in the 2009 Blind Analysis Contest of an E-Defense shaking table test on steel frame building with damper which was held by the National Research Institute for Earth Science and Disaster Prevention. It won the award as the finest team in the two categories out of four.
For more information
http://www4.kke.co.jp/stde/en/awards/index.html
KKE simulated how factory A would react towards a major earthquake strike under two different patterns. One was "as-is", the present condition without any seismic retrofit, and another was based on a seismic retrofit, which the general contractor proposed. Both results showed that the building will collapse eventually, but the building with seismic retrofit collapsed faster than the status quo.
We were aware that factory A was built on a fairly soft ground, but not too soft that would potentially cause a major liquefaction. We expected to mitigate seismic vibration by satisfying the value of Is over 0.6, but it turned out to produce a contrary effect depending on several shaking patterns. Placing reinforcement members at the upper part of the building produced the building to vibrate stronger.
The other plant that KKE simulated in the past was built up on a hill with solid soil. The simulation results showed that there would be no resonance phenomenon caused by implementing seismic retrofit, thus conducting seismic retrofit for this building was deemed appropriate.
▲ The perspective drawing of 3D analysis model of factory A
▲ Building image with seismic dampers
Receiving the results, we made our final decision by the end of 2014 that we would not introduce seismic retrofit plan for factory A. This also meant that we had to come up with a new design, so we requested KKE to continue with the studies and make some proposals.
The important point was to implement the dampers outside of the buildings. No matter how significant the preventive measures are, that doesn't mean that we could stop the plant from operating and we still needed to keep the production line going during the construction period. This caused the initial plan to require long construction time and high cost.
It was not that saving construction time and cost was our top priority. For each plant, we had BCP (Business Continuity Plan) and studied seismic risks such as possible seismic intensity. Reinforcement with seismic dampers met the performance target which would endure the risks and so we decided to adopt KKE's proposal.
KKE always came up with their best solution, so we wanted to respond to that by confirming step by step, whether it was feasible. For example, there was equipment such as utility facility in the circumference of the factory A which might become a barrier to place external dampers. Thus, we called the person who was in charge of the plant management from our head office so to arrange an environment to install the dampers smoothly.
This was different from outsourcing the entire project to a general contractor and having the work completed in a given time and cost by them. With no precedent case, we had to take detailed steps. It started from having discussions on seismic control, making decisions on basic design, detailed design and then proceeding to the construction work.
Through careful and detailed discussion on the seismic control design, we finally decided to adopt it at the end of 2015 and the work started from the beginning of 2016. Compared with the initial retrofit design, we were able to shorten the period by half including the discussion process and the cost by 50%.
As a footnote, KKE is in charge of only for a few of the buildings, and the others will be taken care by a general contractor. All buildings, however, will follow the reinforcement concept drawn by KKE.
▲ Seismic control devices were placed on the external part of a building,
thus people were able to continue their operation as usual.
I think it's possible. The environment for each location is, however, different so I don't think they can completely adopt the same design. For example, the buildings in Takahama plant had enough space to place the external dampers that would project 4 to 5m from the building. As I mentioned earlier, seismic retrofit is effective depending on the condition of the ground.
We used simulation as a tool, to understand how buildings would respond to a major earthquake strike and what measures would be effective to secure safety. You can decide based on the results if using seismic dampers is better or strengthening the building is more suitable for the particular building. Depending on the circumstances, adopting both methods might be an option as well.
The key is to find the most optimal measure for each structure. I would say customization is necessary for reinforcement. I think that believing without question that a structure is safe just because the value of Is was more than 0.6 is overlooking its original significant purpose.
We did. If we focused on satisfying the Is and strengthening the building, we could say "But we followed the act" even when the building collapsed. What we wanted to achieve was, however, to find a way that ensures the building from collapsing. During the project, an evaluation which a third party conducts for super high-rise building ("evaluation of seismic capacity") caught our attention. It would consume too much time and cost to conduct the similar evaluation for super high-rise building with a plant built 40 years ago with seismic dampers. Instead of conducting an evaluation, we decided to consult with an expert in the field and approached Professor Hideki Idota of Nagoya Institute of Technology who is an expert on structural and seismic safety. We explained our standards and concept for seismic control and got feedback on which points we should be careful with, and reflected to our design.
Yes, that's right. Even if there were an unexpected damage caused by an earthquake, at least we would be able to explain why we took the measure and it was supervised under a seasoned expert. We are considering reinforcement for other buildings based on the same standard and concept.
***3 Due to the unique approach used in this case, it was presented at the conference hosted by the Architectural Institute of Japan in August, 2016.
KKE members really worked with passion. We were taken aback by one of the new proposals, which was deeply thought through but even caused an overheated discussion within our team.
Everyone was convinced that placing the external dampers would work, but it turned out that it's necessary to place one damper inside the building, near to a wall. Then we found an underground tank close to the wall and realized that we could not place a damper above it.
This was a pain in the neck, but also led us to a new understanding that the time and cost were better installing some dampers inside the building rather than placing all dampers outside. This approach is applicable only for buildings with a condition where dampers would not interfere with production facilities, but we plan to take this approach from our next project.
There are a lot of things we learned from KKE through the detailed steps we took for the factory A project. We are more confident, as much as we can make a proposal for factory B using the knowledge we gained.
It is our hope to receive support from KKE until the end of the entire project. I was inspired when I heard its mission was to "create new added-values based on engineering". The same thing can be said with us manufacturers: technology is our strength when we challenge the world. Based on its mission, we wish KKE for further works and contributions to various business fields.
Interviewed in July 2016
Corporate Communication Section
TEL:+81-(0)3-5342-1040
E-mail:i-marketing@kke.co.jp