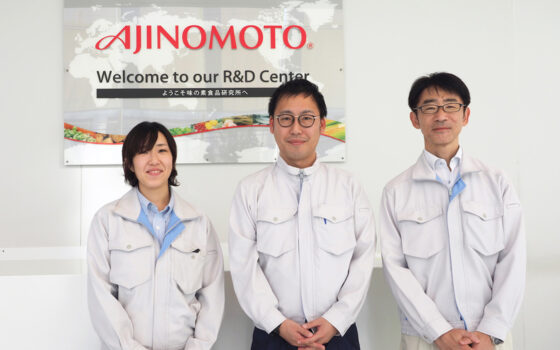
- Supporting Manufacturing
We have domestic factories in three areas: Kakegawa (Shizuoka), Kuki (Saitama), and here in Osaka. R&D is located in Yokohama, where there is a laboratory that is primarily used for formulation development. In addition, each factory has a dedicated team for technology development in order to enhance fabrication engineering. Other than that, production engineering is presided over by the Technology & Engineering Center, whose head office is located at the Kakegawa factory. There are four seconded people working at the Osaka factory, including some who are on loan from other organizations. The Osaka factory purchased Particleworks and we are the ones using it.
To put it simply, our first motivation was that we needed "a picture". It is one of our jobs to suggest plans for the improvement of equipment and production methods in order to manufacture high-quality products effectively. These plans are developed based on various studies and experiments. When we explain such plans to a manager, a picture or a video image that was shot during an experiment is often worth a thousand words and helps illustrate our ideas.
However, not all experiments can be photographed or recorded. For example, when we produce cosmetics, it is not realistic to shoot a video inside a mixing vat so that we can show how compounded raw materials are mixed together. Using simulation software, we can show images and movement inside the machinery, something that is normally impossible using cameras or the human eye, in the form of a simulation. With such simulated images, we can convince the manager in charge of production to accept our plans for improvement just by showing the images and saying, "if we change this thing, this would work like that". The level of persuasiveness definitely increases. Thanks to the images, the manager can understand our plans more intuitively.
It may sound funny, but being able to convince the manager is crucial. Let's say that we are able to convince the manager during the first meeting. By not having to carry out additional experiments, create additional reports, or have more meetings, we are able to save time and money and this eventually leads to faster development. We could outsource such simulation analyses to a third party, but that might mean an inability to request detailed parameters and conditions or to change such parameters and conditions flexibly when required. We would have to accept a limited degree of freedom, and on top of that, the cost of outsourcing simulation analyses would be quite expensive. Taking all of this into consideration, we decided to purchase the software and use it ourselves.
To be honest, I (Dr. Yokokawa) was against using simulation software at first. One of the reasons for this is that I had spent my whole career in laboratories and I have always believed in experiments. I thought that when evaluating something, experiments obtained results more cheaply and quickly. Of course, it's different for the development of products such as automobiles and rockets, where it can be dangerous for people to be at the actual site of testing, but for cosmetics, the important thing is knowing how to combine ingredients, so I used to think that experiments superseded all and that we could learn all we needed to know through trial and error.
"I have the same emotional attachment and expectations
for Particleworks as I did for Macintosh in the old days."
Dr. Yoshihiro Yokokawa
This is very basic, but when you specify certain parameters and conditions for an analysis simulation and run it a hundred times, you will get exactly the same results each time. During actual production, however, raw materials often vary by lot, some more and some less. That is to say, it is impossible to completely replicate the production process by simulation. So at first, it didn't make sense to me to purchase analysis software, and I didn't expect much from it. I just thought that it might help convince upper management at sometime in the future. My low expectations changed when I was able to break the curse of discrepancies between simulations and the real world.
To get right to the point, I realized that the simulation results do not have to exactly match the actual phenomena, something that engineers and specialists familiar with simulation probably already know.
Let's say that we have material A and material B and need to combine them uniformly. We create a simulation model that is as similar to the actual conditions as possible, and run three different simulations as Case 1, Case 2, and Case 3. If the simulation results indicate a better mixture in the order Case 1>Case 2>Case 3, you can assume that the same tendency will be observed in actual production. Even if there are some irregularities in the raw materials, it is obvious that Case 3 is not the best scenario. As I became familiar with Particleworks, I began to realize that simulations were worth running even if they didn't exactly match the actual phenomenon, because they showed the same tendencies observed in the real world.
In the other words, when using simulation software, trying to recreate the actual conditions and specify parameters in every detail is not the most important thing. That is the most useful lesson I learned from Particleworks, as I was not an expert in simulation analysis. If you become obsessed with accurate parameter settings, there will be an enormous amount of data to input, which will take you forever. Instead, I tried to create simpler models and patterns that focused more on the information I wanted to know, which enabled a lower computational load as well as a shorter calculation time to obtain simulation results.
Mixing and fluid flow is what we think about most of the time, so I heard about software dealing with such topics on a daily basis. I even knew about Particleworks when it was first released, and did have a feeling that it might be useful in mixing.
"We need to master the mechanism of mixing, and Particleworks is the right tool with high usability.
This is how I convinced Dr. Yokokawa."
Ms. Aya Tanaka
The major reason for selecting Particleworks was its ease of use. The first thing I noticed when I started using Particleworks was that the amount of input data was much less than that for other analysis software. Analysis software for experts has many parameters and settings, such as "Select algorithms from A to G". You wouldn't know which algorithm to choose, unless you were an expert and had a theoretical background. It often happens that you end up forgetting the original objective when performing a simulation analysis. In this regard, I think Particleworks is the most suitable software for evaluating the simple models I mentioned previously.
When software has fewer columns for data input, it is less flexible and less capable. On the other hand, when software has more columns for data input, the calculation conditions can be manipulated to obtain the results you want. With Particleworks, as it is less flexible, such manipulation is difficult.
Well, to repeat myself, one of the benefits of using Particleworks is that is can be used as a tool to convince people in charge of production. At the production site, everybody is busy producing their assigned quotas every day. Even if we went to the production site and said, "We obtained such-and-such a result from our experiment, so please try it this way", that wouldn't be enough for them to stop production and change the production procedure for a trial run. Even I would doubt my own proposal, since I couldn't fully explain the images in my head with words only. However, if I have reasonable simulation data included in my proposal, they would react differently. "I understand. Let's try that way." Since we introduced Particleworks, cases like this have been on the rise.
Nevertheless, production engineering is a continuous loop of trial and error. If we were able to shorten the amount of time spent convincing the production site to try a trail improvement from one week to two days, the overall reduction in R&D would add up, and the overall savings would be enormous. The faster we improve the failure rate, the more we can contribute to the company in terms of profitability.
Lipsticks, which are slightly sharpened at the tip, are uniquely shaped to conform to the shape of the lips when applied. However, this unique shape has always been a problem during production, because the sharpened top often ends up with small bubbles inside. These bubbles are generated when the highly viscous lipstick material is poured into a lipstick mold. So we ran several simulations on filling the lipstick mold using Particleworks. The simulation results indicated that the bubbles could be reduced substantially under certain conditions.
After seeing the simulation results, an engineer at the production site implemented a workaround, which successfully reduced the amount of bubbles formed during actual production. The failure rate for lipsticks was reduced to less than one-tenth the number before the improvement was implemented. Later, the engineer who made the change told us happily "The number of defective products has really been reduced!"
Without Particleworks' simulation results, the engineer wouldn't have been able to implement the workaround. Even if someone is intuitively aware of a better production method, it requires time, effort and money to actually implement a change, and typically, in the end, nothing is changed.
▲ A Simulation result: Filling a mold with lipstick material
Well, other than that, Particleworks helped us select new equipment for the production site for two-color foundation. Two-color foundation requires highly challenging production skills. The two materials have different physical properties, such as viscosity, and we have to pour them into a container and create a straight boundary in the very middle of those two materials. Before we used Particleworks, trained engineers used to adjust the pouring position and flow speed in accordance with the fillings and then surfaced the products; that is to say, production was managed by experienced craftspeople. After we ran a simulation on Particleworks, however, we modified the function of certain equipment and were able to automate the production process.
As this use case shows, we may encounter more such cases of analysis software being used to support the introduction of production equipment that does not require experienced skill in the near future. As a matter of fact, it is not realistic to expect that local engineers at foreign production sites will have such experienced craftsmanship.
I'm sure that more staff members in Shiseido factories are aware of analysis software than before. However, we haven't received any such voluntary requests yet. Currently, some members do ask us to run simulations, but they are mostly people who used to work at a production site and then transferred to an engineering development team. Production members would ask such transferred staff for advice, and they would forward the questions to us. On other occasions, we have walked around production sites looking for problems to solve or directly asking the staff, "Can I help you?" Even for trivial things, simulation results can be surprisingly useful, and people at the production site are very happy when they can make effective improvements.
Referring back to what I told you about experienced craftsmanship, staff members at production sites endeavor to overcome impracticability and somehow manage mass production. Even if they don't know what is going on in the mixing vat, at the end of the day it doesn't matter as long as they can produce products without defects. There's no need to conduct simulation analyses if we are satisfied with the current situation. It is also true that we must deploy these technologies when we seek to produce products that fully satisfy the targeted quality. I think that Particleworks is, after all, a tool to create value in the next generation.
There are many unanswered questions on the mixing of water and oil, and we don't yet fully understand what is happening inside. For example, homo mixers, general equipment used for mixing, have rotating blades to create a mixing movement. These blades are hidden by jackets, and rapidly rotate to push the materials through extremely narrow clearances. Due to such structural characteristics, sampling or component analysis is impossible. I have always wondered what was really going on, and started looking into it. However, even though I wanted to carry out experiments and evaluate the process, I had no way to perform measurements. Then we started using this analysis software, which is capable of studying the internal phenomenon.
Once we understand the mechanism of mixing, we will be able to consolidate a concrete process of homogeneous mixing, which would at the same time be variable data for product development for machinery manufacturers. It would contribute to the functional improvement of Particleworks, too. We, together with KKE, are currently running Particleworks on a supercomputer. I'm very hopeful that we can achieve a positive outcome.
▲ A Simulation result: Mixing simulation for milky liquid
Particleworks is definitely user-friendly software. It is easy to use even for those who aren't experts in analysis. To put it another way, non-experts can conduct analyses using Particleworks, but for many scenarios, they require technical support and help. KKE provides a satisfactory support system. I really mean that. We will probably be asking you for more help in the future, and we hope to continue working with you.
Interviewed in January 2015
SBD Products & Services Dept. SBD Engineering Dept.
TEL:+81-(0)3-5342-1051
E-mail:sbd@kke.co.jp
Web:https://www.sbd.jp/