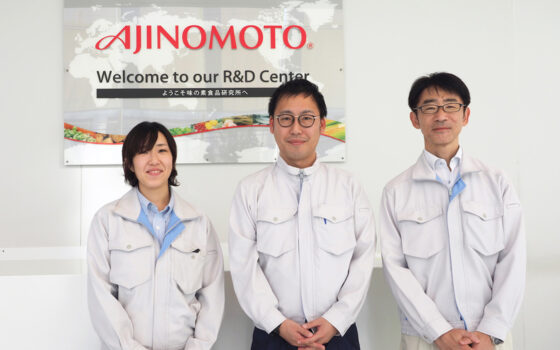
- Supporting Manufacturing
The team for tire production engineering uses FACTOR/AIM to conduct simulations when studying production facilities and systems.
The Production System Technology Department, where I belong, works on developing "production-control systems" and "production information visualization systems" for tire manufacturing plants. Simulations are used to design those systems.
Production-control systems control "what" and "how much" we produce. Our system-design engineers use simulations to understand the overall flow to facilitate the design process. This helps implement the PDCA cycle faster.
Primarily, we use it to validate the specifications, ascertain the limits, and verify negative effects in the event of malfunction, etc. before we introduce the actual system.
With the actual system, it is not easy to conduct extreme verifications that might cause malfunction. That is why we use FACTOR/AIM to conduct simulations. We need to investigate beforehand "how much each parameter has to be changed before malfunctions occur," "how frequently each failure has to occur before production is severely affected," and so on.
Basically, each engineer in charge can use the simulator for verification whenever they need.
Fig.1 FACTOR/AIM Parameter Setting Screen (General Model)
Recently, we have begun linking actual logics and FACTOR/AIM. For example, in the manufacturing plants where human operators are transporting intermediate materials on power vehicles, we use FACTOR/AIM to verify a system that provides optimal transport instructions to the operators.
We used to develop an abstract model then loaded it into FACTOR/AIM to verify the whole system. The model was based on existing logics operating in the manufacturing plant. However, the logic has already been working on FACTOR/AIM, so the new idea is to load only the portions that require modeling into FACTOR/AIM and then link the logics on FACTOR/AIM.
To develop a model is to abstract the logic. In other words, the model is different from the actual logic. This means that we are able to verify the actual logic with an abstract model on FACTOR/AIM regardless of the model's validity.
Fig.2 How Logics and FACTOR/AIM Are Linked (Image)
I have long used the approach of setting FACTOR/AIM to record "values of interest" regarding a large model and then plotting the recorded continuous values in a graph or isolating changes to those values and analyzing them using spreadsheet software. On the screen of FACTOR/AIM, it shows us "usage rates" and "other values" next to "resources" such as manpower and machines, and we can track changes as necessary.
It also enables us to check the usage ratios of resources changing each time. We can easily see what is happening in the manufacturing plant, because we can understand changes numerically even if such data is not actually tracked from the applicable production line in the manufacturing plant.
The greatest feature of FACTOR/AIM is the ease of creating models.
We use a simulator when we are struggling to find an answer. A simulator is a tool to repeat the process under a given condition in order to find an answer. This process must be repeated until we find an answer, but with FACTOR/AIM, we can complete a number of verifications in a short period of time because it is very easy to change the parameters and conditions.
Various types of simulators are available in the market, and some software programs have cool visuals using computer graphics. However, those simulators require huge amounts of time just to create models, and they do not have the ease of FACTOR/AIM has when running repeatedly for verification.
The modeling process of FACTOR/AIM is also easy for us because of its simplicity and convenience. We can create small-scale models on our own by creating resources on FACTOR/AIM and combining them on the "Process Plan", which is a screen when we define flow of items such as the process analysis chart.
Fig.3 Example of Modeling in FACTOR/AIM
It takes time to create a large-scale model, even with FACTOR/AIM. When we have to create such a model, we ask Kozo Keikaku Engineering to do the modeling for us. We use a simulator to find an answer quickly.
Kozo Keikaku Engineering can create models faster than we do, so we have trusted them. We find your service very useful because you understand our requests and come up with precise solutions.
Fig.4 Example of Large-Scale Modeling with FACTOR/AIM
At Bridgestone, we use different simulators for different occasions. For presentation materials, we use one that generates a variety of computer graphics images for better, more intuitive understanding.
We like the fact that the simulation result is produced immediately after starting the simulation and models can be changed easily.
The recent version adopted the flow view of the Process Plan screen, which shows us the movements of resources. It makes us grasp the overall flow very easily. At manufacturing plants, production process is divided and frequently combined. Thanks to the flow view, we can understand those changes intuitively.
The easy-to-see, easy-to-understand outputs are helpful when we review them. Simulations are different from day-to-day operations. Sometimes the next simulation session is a year away. Our skills improve during a session as we run simulations repeatedly, but once the session is over and we do not use the simulator for a while, we sometimes forget how the models were made. In these cases, we often open and check the files we created in the past.
Fig.5 Fig. 4 Modeling Example of FACTOR/AIM
"Simulation lets us find clues to solve problems that involve phenomena and movements that are difficult to reproduce physically."
The essence of simulation is to test many different patterns repeatedly in order to find an answer. It is difficult to conduct verifications in the real world by mobilizing people and moving physical objects, but simulation enables us to see an answer gradually by repeating the evaluation of "how the change affects to anywhere else." The most important aspect of simulation is that it enables us to recognize things we have not thought about before, and to find answers.
Unexpected results can be obtained by trying out different parameters, and thinking about those results helps the design engineers improve their own skills. After running countless simulations, we learn many things. Over time, we have become adept more at estimating the cause of a problem when the actual system turns out not to work well.
In other words, empirical values are stored in our minds after conducting many simulations.
They help us explain to other teammates. For example, we also assume movements of operators in simulations, but the actual operators may not move as expected. They may insist to do in other, a familiar way. In such cases, we can explain logically how much the efficiency will improve when you move this way we simulated.
Also, when an issue occurs, we have a meeting with teammates from different departments to identify its cause. The participants may speak off the top of their heads because we do not know the answer immediately. However, if the speakers have sufficient simulation experience, they can make comments based on solid facts. Also, the other participates can judge whether a possible cause is "fairly close to the answer."
Due to frequent job rotations, FACTOR/AIM may be used in other departments by those engineers who have learned how to use it even after they are transferred. In the company, any operation has an opportunity to use a simulator.
Bridgestone also uses FACTOR/AIM for internal training of simulation. That is because FACTOR/AIM is the best simulator to help us learn the concept and basic principles of simulation.
We used FACTOR/AIM mostly to develop production systems, but nowadays we use the simulation to design inspection machines, molding machines and other standalone machines.
Bridgestone conducts business globally, and is operating manufacturing plants in more than 25 countries around the world. So in order to operate in the global market, standardization is a key. Of course, we must consider regional characteristics and different product types. We cannot standardize everything. We must determine "how much we should standardize." Specifically, "we must identify the elements that we should be able to control." We believe simulation will be one of the effective methods for us to find the answers by understanding "what outcomes we can make with changes."
Interviewed in November 2012
Overseas Marketing Dept.
TEL:+81-(0)3-5318-3091
E-mail:i-marketing@kke.co.jp