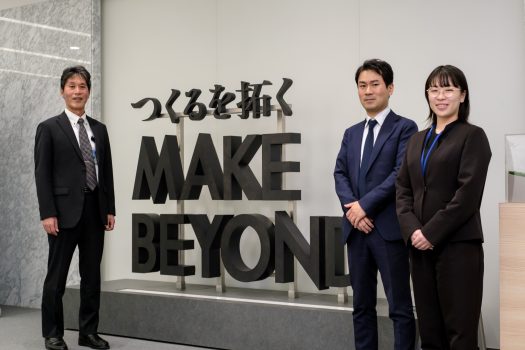
- モノづくりを支える
VAIO株式会社の前身であるソニー株式会社のPC事業部において、2007年頃に導入しました。解析専任者だけでなく設計者にも解析ソフトウェアを展開することでデザインと放熱性能をより多く検討できる環境をつくることが狙いでした。当初はFLOEFDを含む3製品を使用していましたが、設計者目線で使いやすいFLOEFDに集約し、それから現在に至るまで、継続して使用しています。
ノートパソコンの開発期間はおよそ1年程度で、そのはじめの3、4か月の間に、熱解析を行いながら設計の作り込みを行います。その後、3回程度の試作を経て完成へと至ります。
VAIOでは全てのPC製品にFLOEFDを適用して解析を行っていますが、最新の製品は、2024年10月31日に発売したノートパソコンのハイエンドモデル「VAIO SX14-R」です(法人向け名称は「VAIO Pro PK-R」)。カーボン素材を採用しており、軽量で堅牢性に優れるのが特徴の一つです。国内での組み立てや厳しい試験の実施により高い品質を確保しています。
SX14-Rでは、FLOEFDでセットレベルの解析を300回以上実施しています。前回のモデルは約150回だったため、その2倍の量になります。なお解析1本あたりにかかる時間は3時間程度です。発熱箇所は主にCPUですが、他にも電源ICやメモリ、ストレージ、通信モジュールなどあちこちに熱源があります。使用状況によって熱源の組み合わせが違いますし、熱対策の方法も色々あります。温度センサーの位置やファンの回転数、CPUのパフォーマンスの調整などを考えると、検討パターンは相当な数になります。
新機種を開発するたびにCPUの性能は上がります。状況によっては10年前の4倍もの電力を出す状態もありますが、その頃から筐体のサイズは変わらないため、従来と同じくらいのサイズのファンや冷却フィンなどで熱の問題を解決しなければなりません。またノートパソコンは使用中に人が触れるため、温度やファンの騒音の制限が厳しくなります。つまり熱設計の出来が、本来の性能を発揮できるかどうかを決めることになります。
解析例の一つが、排気口が塞がれた場合の検証です(図2)。排気口が塞がれてしまうと内部が高温になりますが、環境温度が高くても内部温度は高温になります。熱解析によって、排気口が塞がれているのか環境温度が高いのかを見分けるための温度センサーを設置する箇所を決定しました。
ヒートパイプの位置関係についてもFLOEFDで検討しました。
SX14-RにはCPUの熱を運ぶメインの2列のヒートパイプと、電源ICの熱を運ぶサブのヒートパイプがあります(図3)。FLOEFDによる事前の検討により、メインとサブのヒートパイプをクロスさせ、メインのほうがより広い面積でフィンに接するような配置が適切であると提案しました(図4)。クロスさせないほうが製造には適しているため両方が試作されましたが、最終的にクロスするタイプが採用されました。
熱設計には試作段階でブラッシュアップをして理想に近づける分野もありますが、ノートPCの熱設計は逆で試作前の構想設計段階で仕上げるのが理想です。試作段階では既にスペースが確定しているため新しいアイデアを盛り込む余裕はありません。問題が起きれば、対策を追加しコストや重量が増えたり、CPUのパワーを早めに抑えたり、ファン騒音を妥協したりすることになってしまいます。このように試作段階では問題に対して応急処置的な対応が中心になるため、製品の理想像から離れていってしまいます。そのため最初の構想設計段階でいかに完成度を上げて、試作段階の変更を少なくしていくかがとても大切になります。
例えば、底面ケースの温度分布で、解析の温度コンターとサーモグラフィの熱画像を比較して精度を確認しています(図5)。温度分布の様子がよく一致していることが分かります。このケースの検討段階では、FLOEFDで樹脂筐体やアルミ筐体も含めて様々な検討を行いました。
SX14-RではCFRTP(Carbon Fiber Reinforced Thermo Plastics、炭素繊維強化熱可塑性プラスチック)を採用しています。繊維の配向や層構成等を放熱に有利な組合せにして従来機種のCFRPやアルミ筐体よりも高い放熱効果を発揮しています。このように、底面ケースは放熱に関して重要な部分であるため、高精度な解析が求められます。
7月に発売されたモバイルディスプレイ「VAIO Vision+ 」の熱設計においてもFLOEFDを活用しました。周辺機器は以前から当社で取り組みたいと考えていたテーマであり、今回実現に至りました。世界最軽量ですが、それ自体を狙ったわけではなく、「いつでもどこにでも持ち運んで自分の作業領域を広げる」というモバイルパソコンと共通の思想をベースに企画された製品です。 当初はそれほど高温にならないと考えていましたが、試作が始まってみると思いのほか発熱して対策が必要になりました。画面サイズを調整するスケーラーICや基板の配線からの発熱が大きかったため、内部に高熱伝導のグラファイトシートを敷いて対策しました。もともと筐体が薄いことから難易度が高く、FLOEFDで確認しながら、シートの場所や大きさを検討しました。
FLOEFDは主に試作前の段階で使用しますが、実機評価の段階でも役に立っています。
従来は試作時に熱の問題が発生してスケジュールに余裕も無いときは考えられる対策の「全部盛り」をやっていました。つまり、どの対策が効いているのか、また原因が何なのかはっきりしないままだったのです。ですが、試作機での対策と並行してFLOEFDで解析を行うことにより、熱の問題が試作機内部のどこに起因しているかが分かり、対策案を絞り込むことができるようになりました。
また、メッシュをかなりラフに切っても解析できる点はとても気に入っています。
設計の現場では、大体で良いので今すぐ解を知りたいということがしばしばあります。他のソフトウェアだと、メッシュをきちんと切らないとまともな結果が出てこないことも少なくありません。粗いメッシュでも結果が出ると、例えば、さっと簡単な解析を流して結果が出ることを確認したうえで帰宅前に本解析をスタートし、次の日出社すれば結果が出ている、といった使い方も可能です。他のソフトウェアに触れる機会もありますが、やはり設計者自身が使うという視点に立つと、FLOEFDの使いやすさは圧倒的だと思います。
CADにアドオンしているため、解析用モデルを作成しやすいこともFLOEFDの大きなメリットです。メカ設計から受け取った3D図面のままだと色々とエラーが出ます。アドオンであれば、それらのエラーの修正や自分でパーツを作る際にもパーツの作成が容易にでき便利です。
やはり、もっと解析の回数を増やしていきたいですね。
限界までPCの性能を引き出すためのアイデアを考えると、とても300パターンでは足りません。これは、日々多くの課題に直面している設計者本人が解析を行えるからこそ、出てくる展望だと考えています。きっと解析専任者の方が個々の解析は早く解析出来るのではないかと思いますが、専任者では300回解析する時間があっても課題を300個出せないのではないでしょうか。
また設計から専任に依頼するとしてもきっと課題を絞らなければならないでしょう。 FLOEFDで設計者自身が解析できるからこそ、様々な可能性を検討し、高い製品機能の実現に貢献できるのだと考えています。
取材日:2024年11月
VAIO株式会社について
創立 2014年
本社所在地 長野県安曇野市
ホームページ https://vaio.com/
Simcenter FLOEFDチーム
TEL:03-5342-1046
E-mail:sbdseminar@kke.co.jp
Web:https://www.sbd.jp/