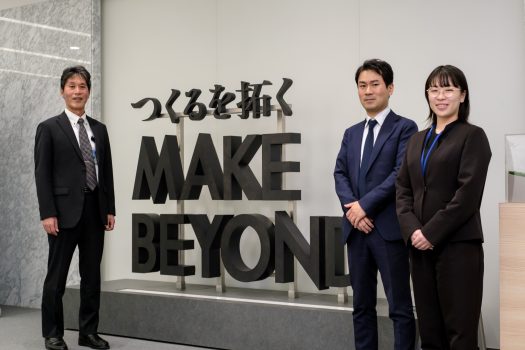
- モノづくりを支える
当社に入社したのは、5年ほど前です。それまではFA関連メーカーで、主に設計に従事していました。その職場でも3次元CADソフトのSOLIDWORKSを使っていたので、KKEとのお付き合いは前職からになります。
当社に転職した当時、3D CADを本格的に活用し、CAE(Computer Aided Engineering)も立ち上げようというタイミングだったのです。そのプロジェクトをスムーズに遂行させることが、私に課せられたミッションでした。当社にはすでにSOLIDWORKSとは異なる3次元CADが入っていましたが、なかなか設計者たちが2Dから離れようとしない、というのが現場の状況でした。
そこでまずは、シミュレーション関係から手を付けようと。使い慣れているSOLIDWORKSを会社に導入してもらい、とりあえず設計は2Dのまま、構造解析の「3次元化」を先行して進めました。
▲3DCAD推進室 室長
土橋美博氏
一番は、機械の軽量化です。剛性を保ちながら軽量化を実現するということは、すなわちそれだけ材料を減らし、コストを削減できるということ。輸送面でもメリットが期待できます。当社のように“重厚長大”なモノづくりをしている会社にとっては、それが大きな強みになるのです。
はじめに取り組んだのが、SOLDWORKSのオプション機能を活用したトポロジースタディです。しかし、そのトポロジースタディも順調に進んだわけではありません。スタディの結果求めた形状を再度構造解析しようとしても、うまくいかないといった問題もありました。そんなときに、昨年、KKEから「HiramekiWorks」を紹介されました。説明を聞くうちに、「これは使えそうだ!」と直感したのです。
このソフトはトポロジー最適化だけではなく、形状最適化という手法を使用することができます。例えばメッシュを削るのではなく、メッシュの節点を移動させる手法についても検討できる。その辺りが、素直に面白そうだと思ったのです。
トポロジーでも、「削って解析」を繰り返せば結果は出せるはずですが、それには膨大な時間がかかってしまう。メッシュそのものを自動で動かしてもらえるのなら、その時間を短縮することができます。また、形状最適化はメッシュ節点を動かす手法であるため、詳細な応力制約を設定して計算することができますので、設計の多くの場面で使用することができるはずだ、と。
そうです。「100% 使える」というより、「もしかしたら、30%、40% の“何か”があるのではないか」という感覚に近かった。金属の3Dプリンターが急速に市場を伸ばすといった現状を見ると、この世界でも近い将来、パラダイムシフトと呼ばれるような技術の大変革が起こるかもしれません。その時になって慌てても遅い。こうした画期的なソフトを導入するのに、早過ぎることはないと思ったのです。
実際、「K・K・D(勘・経験・努力)」だけで仕事がもらえる時代ではなくなっているのは確かです。転職当時、設計者に「この装置のこの部分は、どうしてこういう形なのか?」と質問をすると、ほとんどが経験をもとにした答えで、理由がよくわかりませんでした。それでは、新しいものはつくり出せないし、次世代への技術継承もままなりません。
これから私たちのような装置産業に求められるのは、より高機能なものを短納期かつ安価で提供することです。そのためには、構造最適化技術やシミュレーションを高度化、多様化させつつ、きちんとしたエビデンスを求めていく体制が不可欠になるでしょう。「HiramekiWorks」は、その重要なツールになり得ると考えました。
先ほどの目的に照らせば、主力製品であるラビング装置を、既存の設計から約26% 軽量化できるというシミュレーション結果を得ることができました。鋳物材料費に換算すると、1台あたりおよそ58万円のコストダウンです。あくまでもシミュレーションの段階なのですが、「ソフトをこのように使えば、こういうことができる」 ということが、よく分かりました。
実は、液晶ディスプレイの市場動向もあって、その解析結果に基づいて実際のラビング装置を製造するか否かは、今のところ決まっていません。ただし、当社もいつまでもラビング装置で稼いでいけるとは考えておらず、今回のトライアルによって、この技術が他の新たなモノづくりに応用できる、という確信も得ることができました。実はそれが一番の成果だと考えています。
▲ラビング装置(参考)
自動車メーカーの担当者なども聞きにいらっしゃいました。やはり軽量化に対するニーズ、悩みは幅広い産業分野にあって、このソフトの可能性に対する期待値の高さを改めて感じました。
社内的なことを申し上げると、現状、このソフトを使ってシミュレーションを行えるのは、私だけ。「こうやって使うのですよ」というマニュアルは必要ですが、それを鵜呑みにしても、必ず最適な製品がつくれるとは限りません。どうやって後進を育てていくか、真剣に検討しているところです。
「HiramekiWorks」に関していうと、解析結果をスムーズにCADデータ化できないものか。それと、ネットワークに接続していなくても使えるようにしてもらいたいです。
これは切なる願いです。1 年で目に見える成果が出せたのは、KKEのしっかりしたフォロー体制があったからこそです。今後とも、変わらぬサポートをよろしくお願いします。
取材日:2019年7月
株式会社飯沼ゲージ製作所について
創立:1962年
本社所在地:長野県茅野市
ホームページ:https://iinuma-gauge.co.jp/
SBDプロダクツサービス部・SBDエンジニアリング部
TEL:03-5342-1051
E-mail:sbd@kke.co.jp
Web:https://www.sbd.jp/