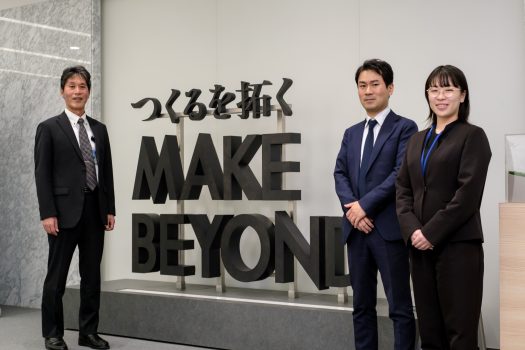
- モノづくりを支える
一般公開されている本社3階のデンソーギャラリー
電子技術部ではエンジンを制御するECU(electronic control unit)の企画開発を行っています。
FloTHERMをはじめて導入したのは2006年ですが、その少し前からエンジン制御ECUが、それまでの車室内からエンジンルーム内に搭載されるケースが出てきました。(※)
エンジンルーム内は車室内と比べ熱環境が20~30℃上昇しますから、熱設計が格段に難しくなります。ノートPCをエンジンルームに置くようなイメージになるのですが、そもそも筐体内部が熱い上に高温に設置することで半導体の寿命に関わってきます。
当初は試行錯誤しながら対応していたのですが、今後この傾向は加速することが予測され、この対処法で間に合わなくなるのは目に見えていました。
そこで、熱解析シミュレーションによるフロントローディングの確立が必要だと考え、検討を開始しました。 2006年に1ライセンス導入し、現在は9ライセンスを活用しています。
※ドアロックのECU、エアコン制御のECU、ナビやオーディオ制御のECU、またエアバックのECUなど以前はなかったものが標準装備されるようにもなり、他にも車間距離を測るレーダーなど安全対策に特化したECU等、高級車では100台のECUを搭載するものもある。車室内にあることで目的を達成するECUもある一方、車内の混雑化の解消やエンジン用ECUはエンジンの近くにあったほうがよいという見解もあり、エンジンルームに搭載されるケースが増えている。また、ECUと機器本体を接続するワイヤーは重量があるため、ECUと機器を近づけワイヤーを短くすることで、全体の軽量化にも寄与できる。
熱マネージメントの要素と時間削減効果
展示会でFloTHERMが電子機器に特化した解析ができることを知り、 他の熱流体解析ソフト何点かと比較検討の上、FloTHERM導入を決めました。
FloTHERMを選んだ理由は以下の3点です。
1.電子機器に特化した解析ソフトであること
それまでも社内には熱伝導に特化したシミュレーターはありました。しかし、20~30℃もの温度上昇を熱伝導だけでは逃がしきれません。 そこで放射による放熱の検討を始め、熱の流れがみえる高機能ソフトを探しました。
当時社内で行っていた熱解析は、発熱体として数種類の半導体モデルが有り、そこからどう熱が広がるかを解析するものがほとんどでしたが、電子機器の場合、500-1000素子もの発熱体が小さな筐体に収まっているという環境ですから、それでは前提が違います。 FloTHERMは、そのような電子機器の環境に対応していました。
2.実験の置き換えになるほどの高精度解析の可能性があること
到達目標は、実験の置き換えになるくらいの高精度シミュレーションです。 具体的には、実測との誤差10%以内での設計を目指しました。そこまでの高精度が狙えるソフトはFloTHERMしかありませんでした。
3.CADと親和性があること
将来の自動化を見据え、これまで蓄積してきた基板設計CADのデータを活用できることは重要です。 その点でもFloTHERMしか選択肢はありませんでした。
最初から目標値を高く設定したので、時間がかかることは覚悟の上でのスタートでした。
導入から1年で誤差30%になり、実用化への手応えを感じました。そして2年で10%を達成しました。 そこから量産の工程に落とすまでに更に1年かかりましたから、最初の1台が実用化するまでに3年かかりました。
FloTHERMを使いこなすためのノウハウが確立していない時から使用を開始しましたので、試行錯誤の繰り返しでした。
まず一番の成功要因であり、かつ一番苦労したところですが、素子のデータを1つ1つ実測したことです。次に、社内の熱実験を集約して技術の蓄積をはかったこと。最後に、エレメカ協調チームで取り組めたことの3点です。
横展開したときに実験とシミュレーションがなかなか合わず、予測していたとはいえ、ここが厳しかったですね。 しかし、考えてみたらあたりまえのことで、メーカーのカタログスペックに依存していたら合うわけがなかったんです。
カタログには保証値が掲載されていることもありますし、データを公表しないこともあります。 カタログスペックからざっくりと出した場合、0.1ワット違えば温度では約3℃の誤差が出ます。 0.3ワットのマージンを持つと9℃も違うことになり、誤差は大きくなります。
そこで1つ1つの素子の発熱量や部材の物性値を実測し、ライブラリ化しました。
また、恒温槽などの計測機もメーカーによって構造が違い、風の回り方も異なり、温度分布が変わってきます。そこにも誤差の原因があることがわかり、測温環境もデータ化しました。 地道に1つ1つを再現し、試行錯誤を重ねながらデータを合わせていきました。
シミュレーション結果と実験値の比較
「3年間で160件の報告書を書き、
それだけの考察を重ねました」
電子技術部2部 担当係長(当時)
篠田氏
当初、熱実験は設計部門で行っていました。2010年からは熱実験業務を開発部署である技術企画室に集約し、全部の測温をするようにしました。
すると、中には必ず10%以上の誤差が出る素子があるんですが、その原因をつきつめていくなかで、モデルの作り方のヒントを つかみました。
実機による実験は年間ではかなりの数になりますから、それら1台1台で誤差を詰める作業を繰り返し、数をこなして見えてきたこともありました。
私たちの試みが部内で認知されて、熱実験を集約できるまでには3年かかりましたが、その下積み期間があったからこそ、どこに出しても恥ずかしくない技術構築ができたと思っています。 ただ、認知されてからは速かったですね。外部で講演もするようになり、協力も得やすくなりました。
熱技術一元化のメリット
成功要因の最後は、電子系の技術者と機械系の技術者の両方がいたことです。うちは篠田が電気系で水谷が機械系です。また、篠田は一時期機械設計に携わっていたこともあります。どちらかだけでは熱のシミュレーションは成り立ちませんでした。
とにかくスピードが速い。量産設計するにあたって、絶対に必要なのはスピードですが、FloTHERMは間違いなく速いです。
たとえば、1週間後にプレゼンにいくからとコンター図まで入れた資料の作成を依頼されたとします。 スペックを聞いて、ECUを設計し、1つの製品で条件を変えて30~50回の計算をします。 計算だけとっても、以前は8時間程かかっていたのが今は半分の時間で済むようになりましたし、 4000万ほどの大規模メッシュで解析できるのは、FloTHERMのスピードがあってこそです。
「金額に換算すると相当な効果です」
電子技術部2部 技術企画室長(当時)
水谷氏
FloTHERM導入前は、実機を作っての評価を繰り返し、量産までには相当の費用と時間がかかっていました。 特に新規性の高いものでは、その回数も嵩みました。
FloTHERMでシミュレーションをするようになってからは、ほとんどのケースで実機評価は2回で充分です。多いときでも5回で済みます。
今はもうFloTHERMなしには仕事が回りません。 素子のデータベースができていますので、2009年当時、モデル作成に1ヶ月かかっていたのが今は2日で作成できます。
高精度シミュレーションを目指しましたので、FloTHERMの開発元(米メンター・グラフィックス社)には多大なご協力をいただきました。解析を進める 上で必要な機能をリクエストしたところ、積極的に対応していただき、来日の時には来社してくれました。
メンター・グラフィックス社に対する提案は相当数書きましたし、それは現在も続いています。
そういう意見も耳にしますが、むしろ全体の底上げを目指します。また、そんなことを言っている場合ではないとも思っています。 日本のメーカーは一致団結して頑張らなければならない局面です。
実は構造計画研究所のユーザになる前、「まだユーザではないですが」とお願いして構造計画主催のユーザ会に出させてもらったんです。
「どうやったらシミュレーションの精度を上げることができるか」、そればかりを考えていた頃でしたから、情報が欲しくてたまりませんでした。
ユーザ会に出てみたら、車のECUを手がけている会社は皆無で、家電・重電・ゴルフ用品や化粧品など多様な業界の方たちと出会いました。
名刺交換しながら、「なぜこの業界で熱対策が必要なんだろう」と思っていたのが、話を聞いてみると、どういった場面で熱対策が必要になるのか納得できるんです。そうやって他業界でのモデルの作り方や試行錯誤の様子をたくさん聞いたことが、ひらめきのタネになりました。
「あ、これをECUに導入したらいいんじゃないか」「これとあれを合わせたらいけるんじゃないか」とヒントがたくさんあって、興奮しました。
構造計画研究所は社歴が長く、構造系にも強みがあるのでユーザ層が厚いです。筐体など他の面でも総合的に相談にのっていただきたいと思っておりますので、今後ともよろしくお願いいたします。
取材日:2012年8月
株式会社デンソーについて
設立 1949年12月
本社所在地 愛知県刈谷市
ホームページ http://www.denso.co.jp
SBDプロダクツサービス部・SBDエンジニアリング部
TEL:03-5342-1051
E-mail:sbd@kke.co.jp
Web:https://www.sbd.jp/